自動車ボディ・フレームの大幅な軽量化を実現する製造システム(STAF)の評価設備が完成しました
2017年09月21日
住友重機械工業株式会社(社長 別川俊介/以下、住友重機械)は、開発を進めておりました自動車ボディ・フレームの製造システム(STAF)の評価設備を完成させ、2017年9月20日に竣工式を行いましたので、お知らせします。
STAF(Steel Tube Air Forming)は、鋼管をプレス機の金型にセットし、「通電加熱→高圧空気注入→成形→焼入れ」の工程で成形加工するシステムです。フレームを組み立てる際に不可欠なフランジ(つば状の部品)を、フレームと一体で成形できることが特長です。従来工法のようにフランジを後から溶接で接合する必要がないため、フレーム剛性の向上、工程の簡略化が可能になります。さらに、フレームの剛性を高めることで、材料の厚みを薄くすることが可能になり、従来の構造と比較して約30%の軽量効果が得られます。
すでに車体部品への適用に向けて自動車メーカーと検討を開始しており、2018年度からの車体部品適用化に向けた設備の導入を目指しています。住友重機械は、STAFを次世代に向けた成長事業として位置づけ、2024年に100億円の売上を目指してまいります。
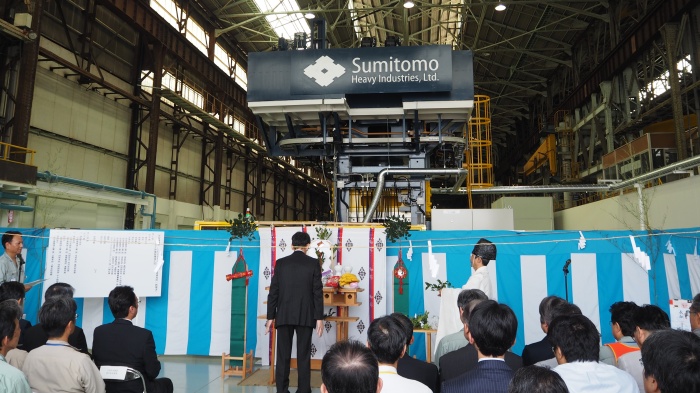
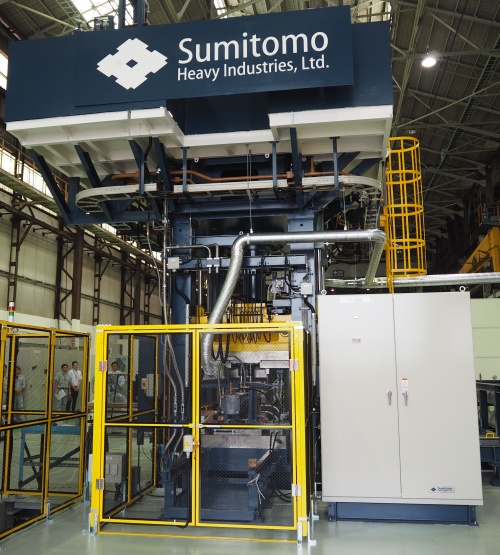
1.通電加熱
パイプを金型にセットし、通電加熱を行います。これにより10秒程度で900℃前後まで加熱されます。パイプの通電加熱は、電極接触面積が左右同じ、かつ、板材よりも安定的に接触させることができるため、均一な加熱が可能となります。さらに、従来の加熱方法である加熱炉方式に比べて消費電力を大幅に削減することが可能です。
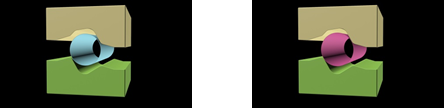
2.フランジ成形
通電加熱後、フランジ部を成形させるため型締め位置(半開き状態)を調整したところで、高圧空気を供給し、半開き状の部分を若干膨らませながら、型締めを行い、フランジ部を成形します。
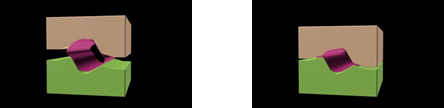
3.本体成形
型締め後、本体部分をさらに金型内面の形状にするために、さらに高圧空気を供給し、ブロー成形を行います。材料が金型に密着することにより、材料が急速に冷却され
1500メガパスカル級の高強度な部材となります。
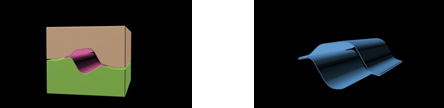
1.30%の軽量化
焼入れされた超高強度部材による連続閉断面構造のため、高強度・高剛性な部材となることから、結果として肉厚を薄くすることができます。同じ強度条件下で、自動車車体の部品をSTAF構造に置き換えた場合、従来の構造に比較して約30%の軽量効果が得られます。
2.コスト低減効果
板プレス加工に必要なブランキング*1やトリミング*2の必要がなく、成形後に端部カットのみであるため歩留まりを90%程度まで向上できるとともに、フランジ付きパイプのため部品点数の削減が可能となり大幅なコスト低減が可能です。
3.シンプルな製造工程(少額投資・省スペース)
板プレス加工で閉断面構造部品を製造する場合は、ブランキング、加熱、プレス、トリミング、そして溶接の5設備が必要です。一方、STAF工法の場合、プリフォーミングの後、加熱とプレスを同時に行い、端部カットするため、3設備で済み、シンプルな製造工程となります。
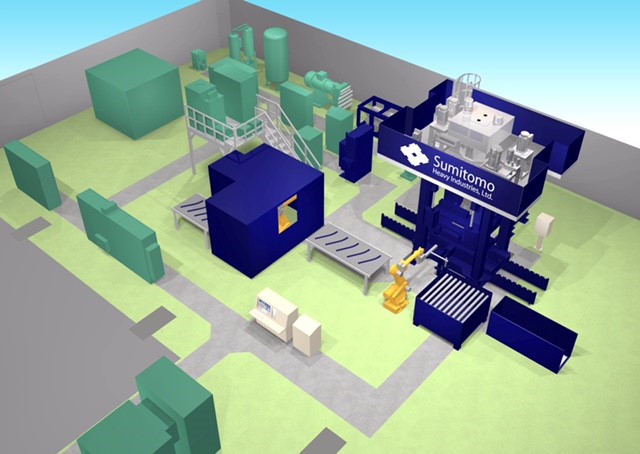
4.高い生産効率
閉断面構造とするまでホットスタンピングの4工程に比べ、STAFでは専用の加熱工程や溶接工程が不要となるため2工程で製造することが可能です。その分、間接工数が大幅に削減でき生産効率が向上します。
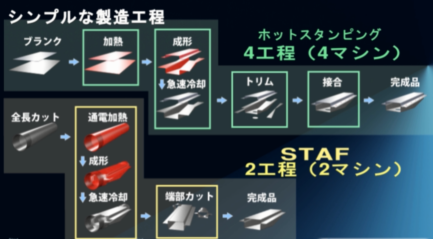
*1プレス加工製品の輪郭形状を作る打ち抜き加工のこと
*2板金や鍛造加工された製品の縁あるいはバリなどの不要なものを切り落とす作業のこと